Midstream Natural Gas Processing
KAHUNA USA STARTS AT THE WELL head
From well head facilities through compression and gathering to treating and cryogenic recovery plants and on to distribution
As the premier ENERGY PROJECT EXECUTION solutions provider in North America, KAHUNA USA has extensive expertise with midstream natural gas processing engineering, design, and project management, including construction management, procurement, as well as regulatory compliance. KAHUNA USA has experience with:
- Gathering systems including dehydration and compression
- Gas processing and treating facilities including cryogenic and mechanical dew point refrigeration, nitrogen rejection, and CO2 and H2S treating, as well as condensate stabilization and carbon capture
- Gas/Liquids takeaway
KAHUNA USA serves as the owner/operator’s engineer–a trusted expert resource. Our project execution team supports all efforts, from upfront capital cost estimating and FEED studies through to successful start-up, commissioning, and operations training. KAHUNA USA provides due diligence, process optimization, and debottlenecking for existing assets.
KAHUNA USA is a full-service engineering and design firm providing cost-effective operations-focused ENERGY PROJECT EXECUTION solutions. KAHUNA USA advocates for our clients and creates lasting relationships by adding value to every project through insightful engineering, project management, and design support. We provide just what you need and nothing you don’t–and we do it well.
KAHUNA USA has the proven ability to execute projects through an EPCM T&M approach, or as a Lump Sum EPC project structure with proven construction partner relationships. KAHUNA USA is committed to working with YOUR desired contract and project approach.
You can count on KAHUNA USA!
We don't just say we get it done, we share how we did it!
REPRESENTATIVE PROJECTS

Stanley Processing Plant
Designed to remove heavy liquids from gathered gas, the Stanley Processing Plant facilitates pipeline delivery to additional processing locations without liquids forming in transportation lines. After processing, the gas was compressed into the supercritical or dense phase for transportation to Midwest gas markets. The client received higher value for the heavy liquids by capturing them away from processing, plus lowered the cost of transportation by eliminating the need for liquid handling in the gathering system downstream of the facilities. KAHUNA USA utilizes intelligent designs to benefit our clients and applies efficient engineering methods for Natural Gas Processing.
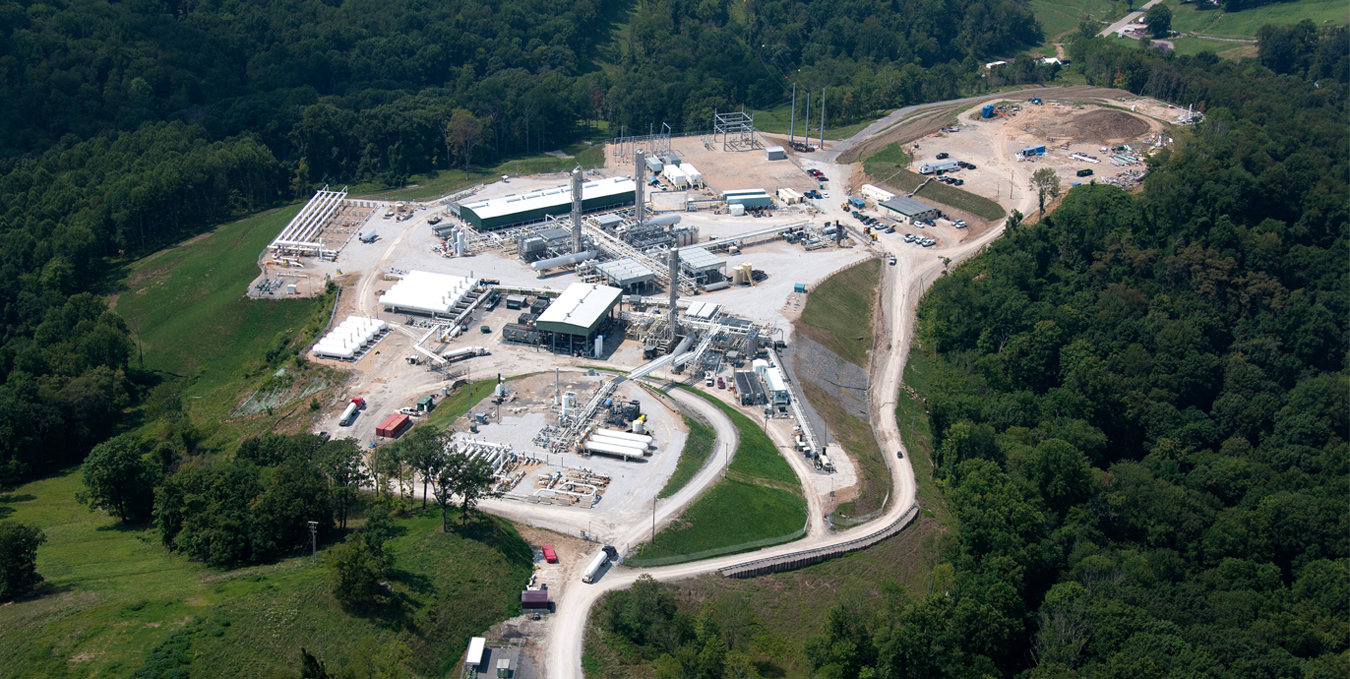
Caiman Ft. Beeler Processing Plant
Built on a hill in West Virginia, the Caiman facility involved a tiny footprint due to site constraints. In addition, the complex was required to build in on 10 weeks. KAHUNA USA designed process equipment in a stacked formation to limit the footprint of the facility and allow further expansion with time. Daily engagement with the client and construction allowed KAHUNA USA to target action items necessary to stay on track, successfully implementing Just In Time Engineering (JIT) to swiftly complete the project.

Battle Ridge Processing Plant
The client needed the inlet facilities operating six months prior to the processing plant coming on line. KAHUNA USA designed standalone inlet facilities remotely located from the balance of the plant to minimize impact on construction. Changes to the inlet facility were incorporated after the plant design was initiated. The result achieved gas flow for the client in the shortest possible time frame.
KAHUNA USA and Tall Oak worked together to get a smaller inlet area online to accelerate gas to market ahead of the full processing facility being online. This provided early revenue to Tall Oak for several months.
This ingenuity exemplifies the agility of KAHUNA USA.
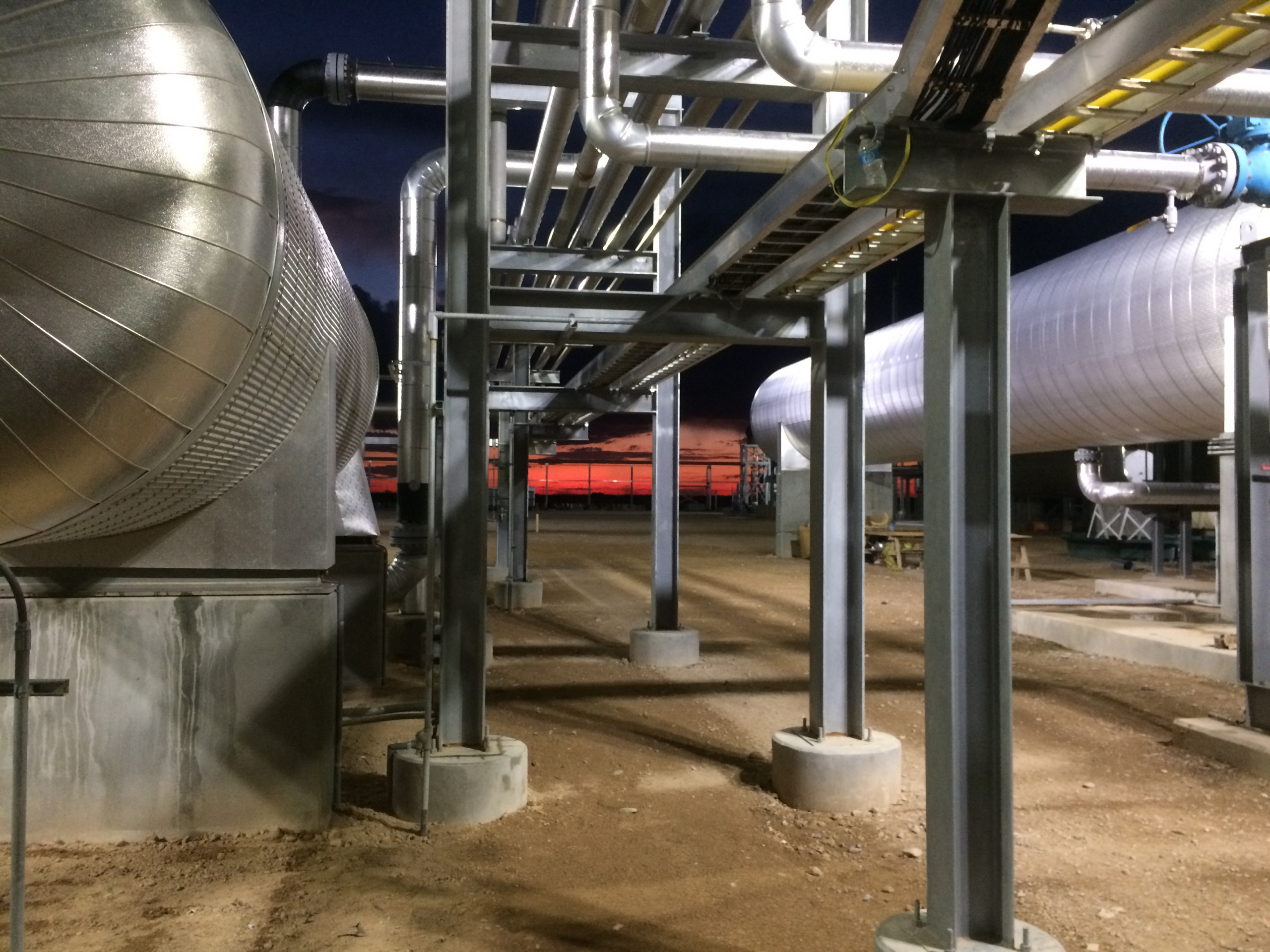
Keystone Sarsen and Bluestone Processing Facilities
Built in Pennsylvania, these facilities had limited access to top gas and liquid markets at the time. Due to constraints on both the gas and liquid takeaway, surplus ethane halted the operations at the facility. KAHUNA USA designed the facility to recover the ethane as an NGL, then used a deetheanizer on the product to recover the ethane. Waukesha was able to utilize the excess ethane as fuel for the compressor engines. The use of pure ethane for compressor engine fuel was a novel concept at the time. KAHUNA USA overcame these challenging limitations to deliver a successful project for the client.
We're here to help you with your Midstream projects.

Jenna Overlee
Business Development
We are here to help. Give me a call.